Process
Through a combination of state of the art machinery together with high-tech process control procedures, we ensure to our customers high quality castings.
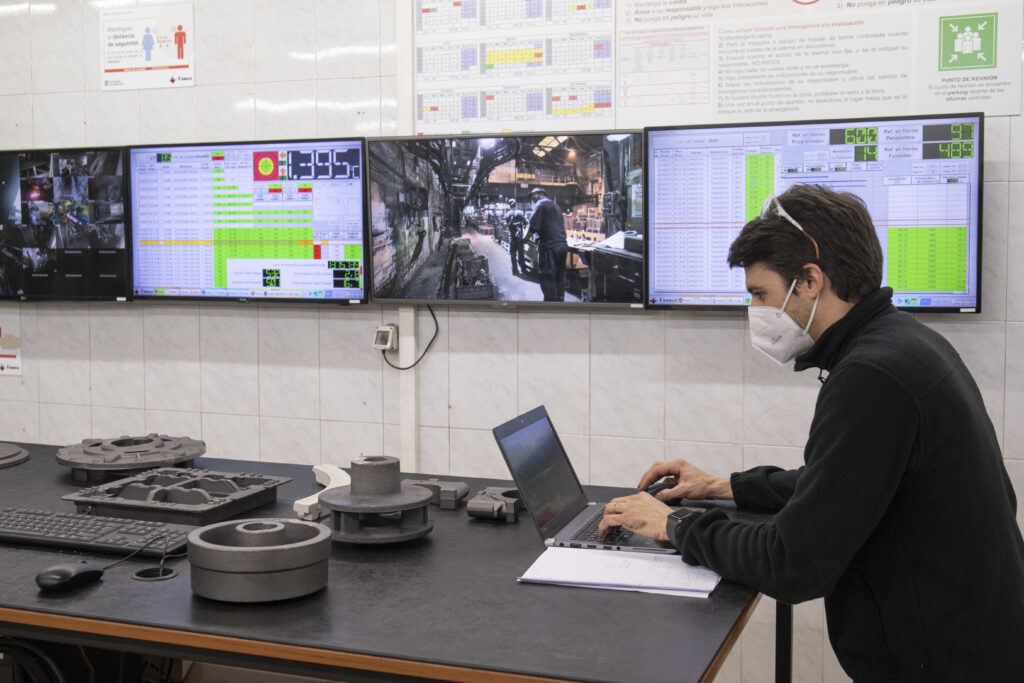
Engineering
In collaboration with our customers, our engineering team participates in the design of the castings, suggesting design improvements to make the parts cast-able at the best cost/quality ratio.
- Design: Solidworks
- FMEA testing: Solidworks Simulation Premium
- Gating system simulation: Novacast Flow&Solid
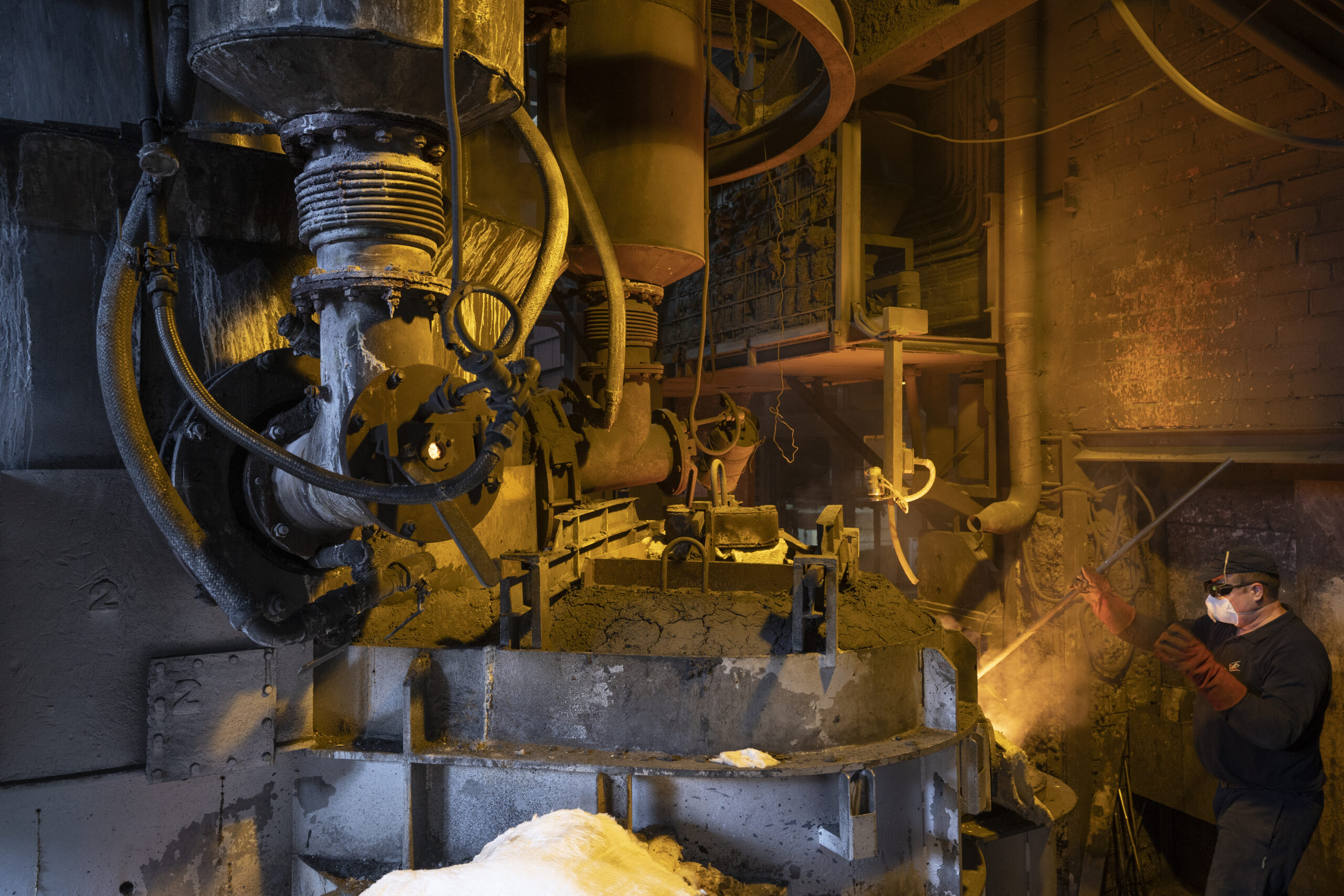
Melting
- 1 Küttner Cupola 20 Tn/h
- 2 Electrical furnaces 7 Tn/h
- Desulphuring unit
- Recarburing unit
- 2 Holding furnaces
- Holding furnaces on each moulding line
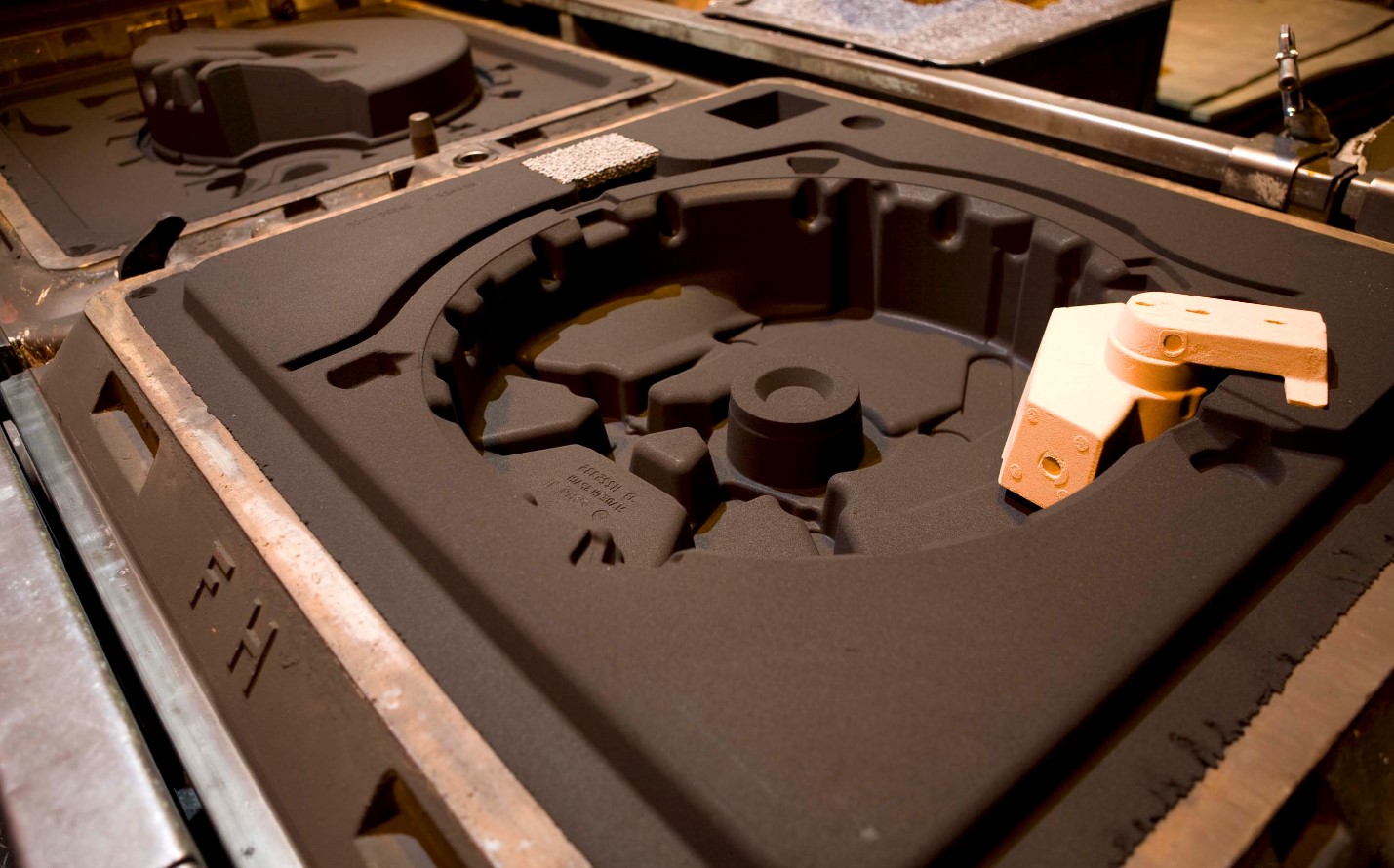
Moulding
- 1x DISAMATIC MK5X (Replaced for DISAMATIC D3Z555 on August 2021)
- Weight range: up to 20 net kg.
- Mould dimensions: 750×525
- 1x HANSBERG (cope/drag)
- Weight range: up to 120 net kg.
- Mould dimensions: 1100x1000x300/250mm
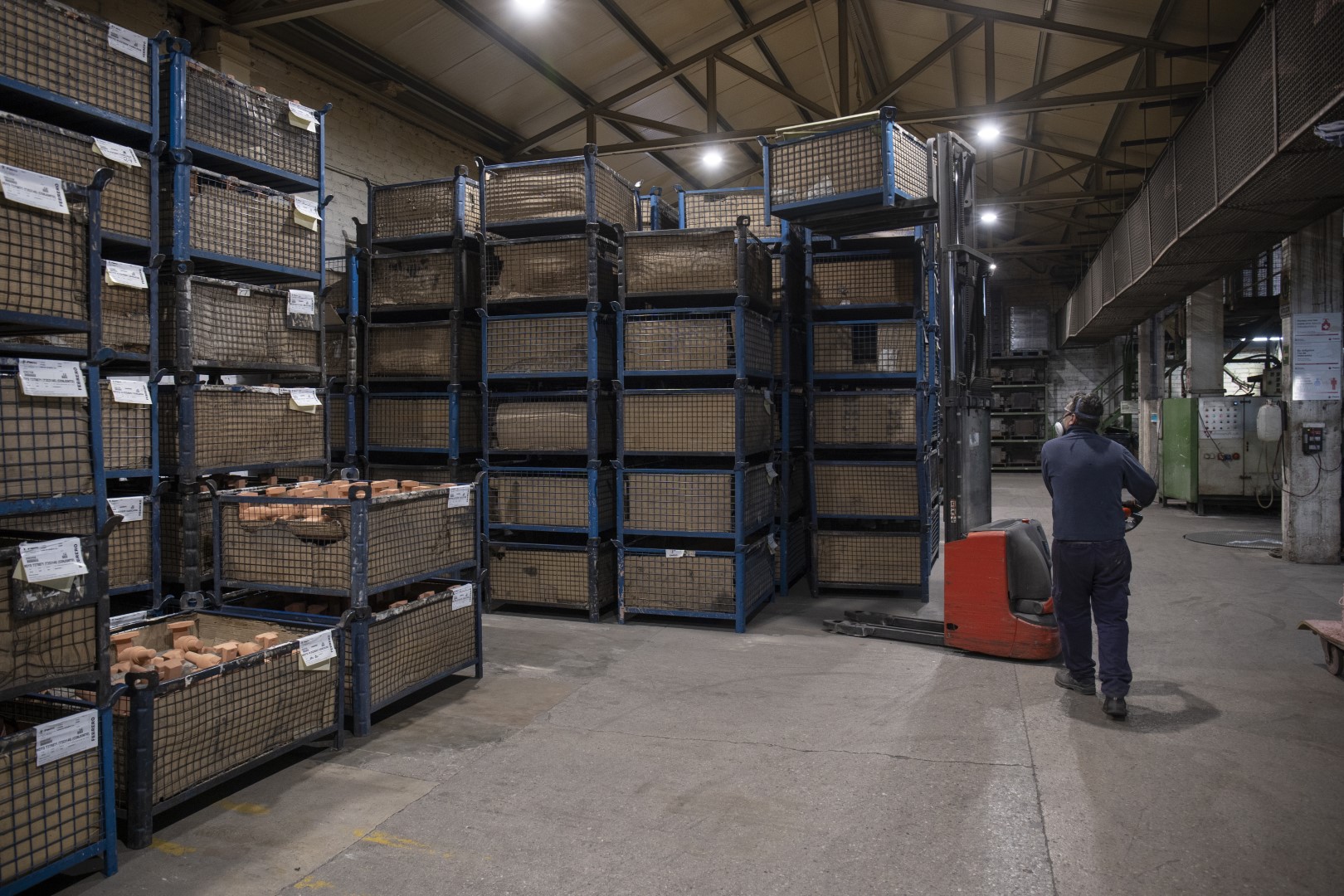
Core-making
- 4 cold box shooting machines
- 1 core painting and drying equipment
- Automatic sand mixing and preparation
- Sand testing laboratory.
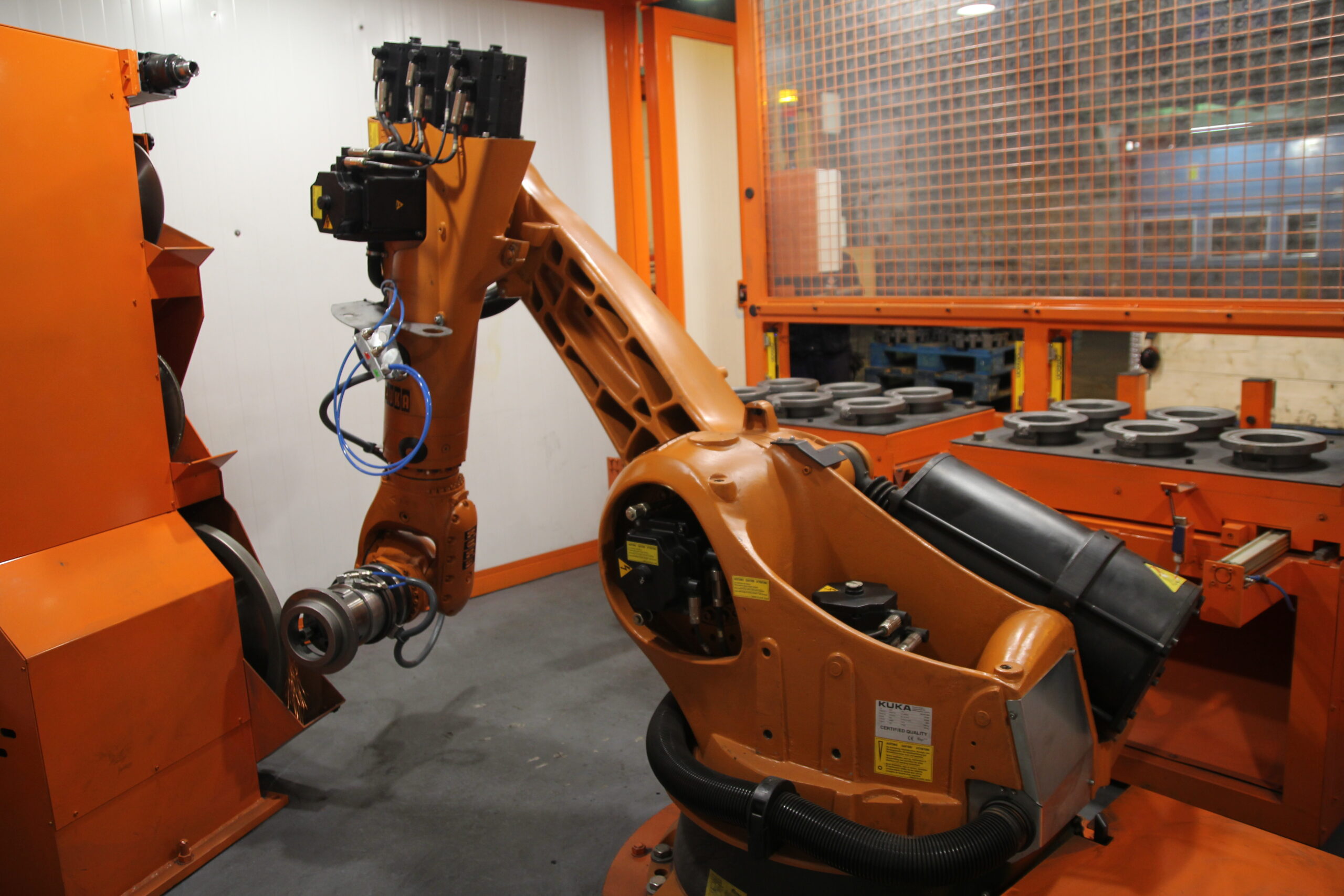
Finishing
- 2 KUKA robots for complete deburring of castings up to 120 kg and diameter of 1.000 mm.
- 2 KUKA robots for complete deburring of castings up to 20 kg.
- 3 MAUS CNC deburring machines (Series 300,600 and 1200) for castings up to 120 kg.
- Stamping die deburring cells.
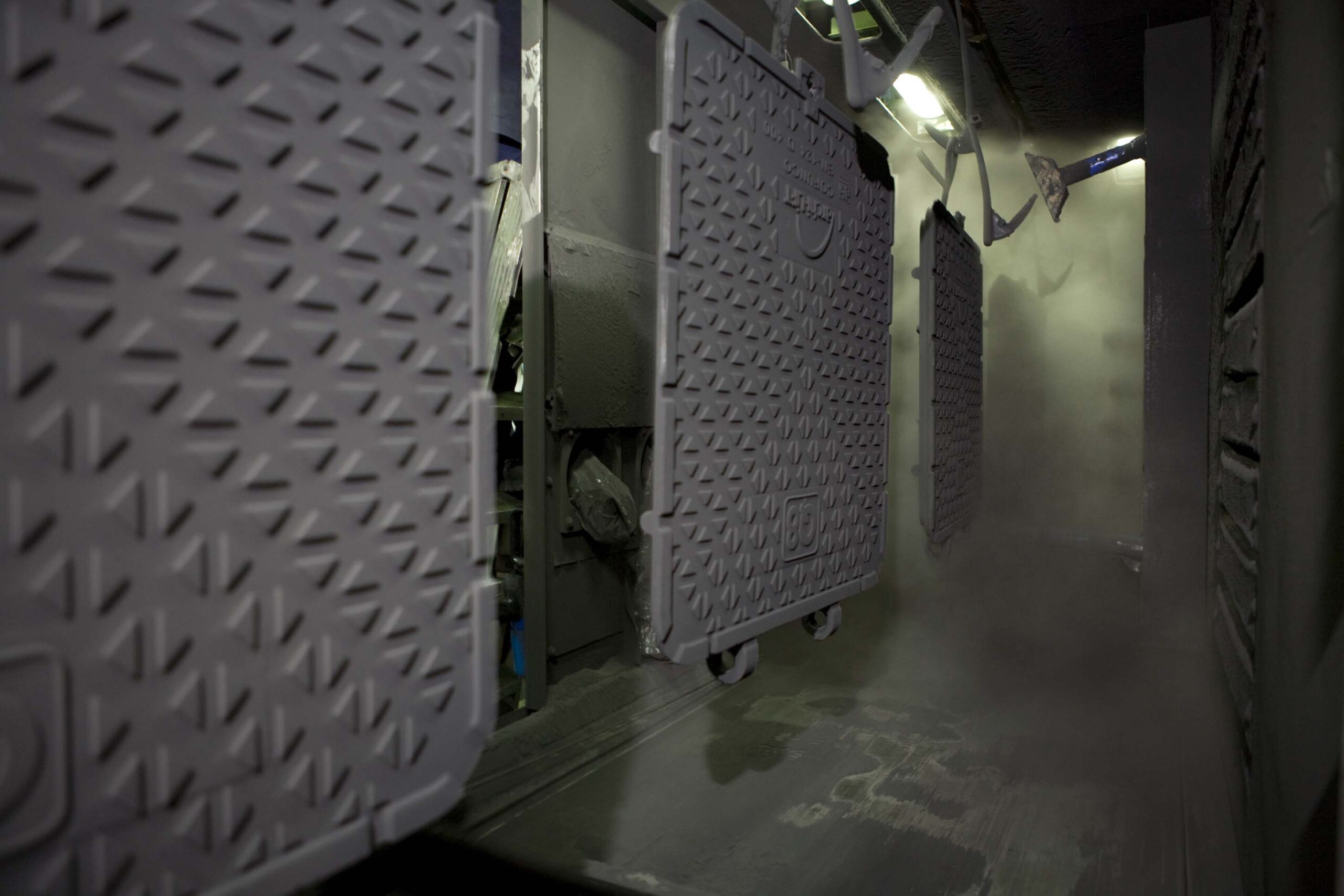
Painting
- In-house epoxy Polyester powder coating (high-quality painting, providing high corrosion resistance)
- In-house water based dip coating (used as primmer).